Crack Growth and Defect Assessment Engineering Services
This study investigated using numerical and experimental techniques to characterise the static and fatigue strength of a flat stiffened panel, designed as a Fibre Metal Laminate (FML) and made of aluminium alloy and Fibre Glass FRP. The full scale panel was tested under both static and fatigue bi-axial loads, applied by means of an in house designed and built multiaxial fatigue machine. The strain gauge outcomes from a preliminary static test were compared with the corresponding numerical results, achieving a satisfactory correlation. Crack propagation in the FML was also simulated. To overcome the lack of experimental information on the size of the delamination area an ‘‘inverse’’ procedure was applied to minimise the numerical and experimental growth rate differences.
Software used
Industry Leading Detection & Prevention For You
BEASY's software products and services help organisations solve complex engineering challenges.
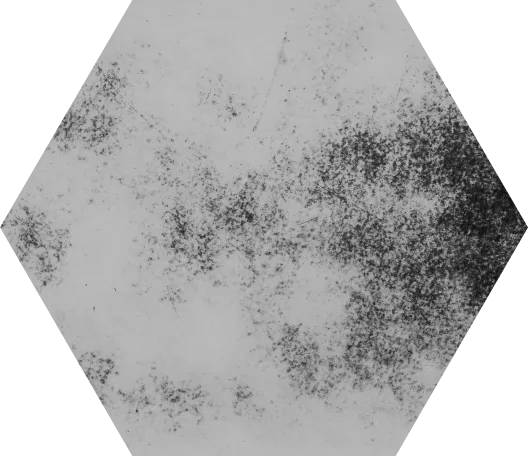
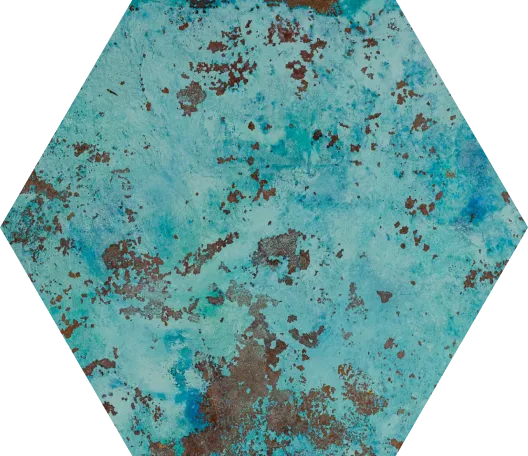